Gravure
Gravure printing is a technique that falls under intaglio printing. The print form is embossed, the printing surfaces are therefore below the non-printing areas.
The predecessor to gravure, the so-called copper engraving dates back to the 15th century. At the time, the motif was manually engraved into the copper plate, but the principle of the remainder of the procedure was practically the same. Gravure itself was discovered in 1890 by a Czech named Karel Klíč. He derived from another of his inventions, the so-called heliogravure. Heliogravure is also based on copper engraving. However, in this case, the manual engraving is replaced by a photochemical process. In the first step, it is a copied photographic negative with the motif on a copper plate. An asphalt and gelatine layer is applied to it and only the printing surfaces remain above this layer and they are subsequently etched using acid. This results in the creation of printing surfaces of different depths. The rest of the process is on a completely identical base to gravure.
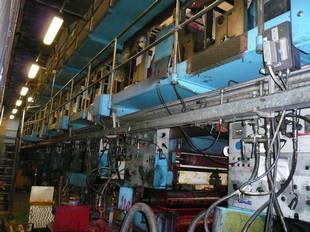
Gravure printing is a technique that falls under intaglio printing. The print form is embossed, the printing surfaces are therefore below the non-printing areas.
The predecessor to gravure, the so-called copper engraving dates back to the 15th century. At the time, the motif was manually engraved into the copper plate, but the principle of the remainder of the procedure was practically the same. Gravure itself was discovered in 1890 by a Czech named Karel Klíč. He derived from another of his inventions, the so-called heliogravure. Heliogravure is also based on copper engraving. However, in this case, the manual engraving is replaced by a photochemical process. In the first step, it is a copied photographic negative with the motif on a copper plate. An asphalt and gelatine layer is applied to it and only the printing surfaces remain above this layer and they are subsequently etched using acid. This results in the creation of printing surfaces of different depths. The rest of the process is on a completely identical base to gravure.
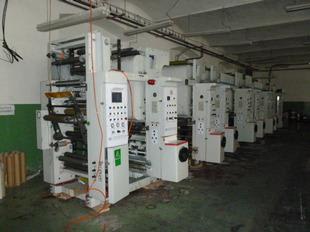
Gravure printing is a technique that falls under intaglio printing. The print form is embossed, the printing surfaces are therefore below the non-printing areas.
The predecessor to gravure, the so-called copper engraving dates back to the 15th century. At the time, the motif was manually engraved into the copper plate, but the principle of the remainder of the procedure was practically the same. Gravure itself was discovered in 1890 by a Czech named Karel Klíč. He derived from another of his inventions, the so-called heliogravure. Heliogravure is also based on copper engraving. However, in this case, the manual engraving is replaced by a photochemical process. In the first step, it is a copied photographic negative with the motif on a copper plate. An asphalt and gelatine layer is applied to it and only the printing surfaces remain above this layer and they are subsequently etched using acid. This results in the creation of printing surfaces of different depths. The rest of the process is on a completely identical base to gravure.
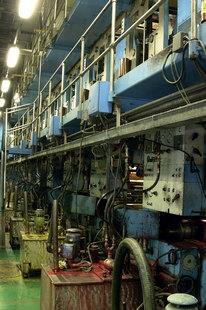
Gravure printing is a technique that falls under intaglio printing. The print form is embossed, the printing surfaces are therefore below the non-printing areas.
The predecessor to gravure, the so-called copper engraving dates back to the 15th century. At the time, the motif was manually engraved into the copper plate, but the principle of the remainder of the procedure was practically the same. Gravure itself was discovered in 1890 by a Czech named Karel Klíč. He derived from another of his inventions, the so-called heliogravure. Heliogravure is also based on copper engraving. However, in this case, the manual engraving is replaced by a photochemical process. In the first step, it is a copied photographic negative with the motif on a copper plate. An asphalt and gelatine layer is applied to it and only the printing surfaces remain above this layer and they are subsequently etched using acid. This results in the creation of printing surfaces of different depths. The rest of the process is on a completely identical base to gravure.